Computer vision enables contactless analysis of the image content through the algorithmic processing of digital images. Objects can be detected, classified, tracked and measured using photogrammetry. Not only ordinary color images from RGB cameras can be used, but also any imaging method – e.g. X-rays or spectral recordings.
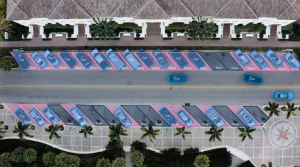
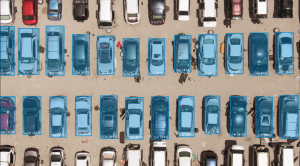
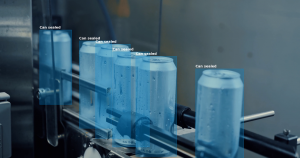
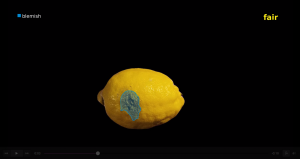
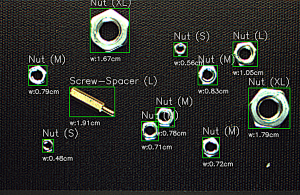
The advantages are obvious – with the help of computer vision and artificial intelligence/machine learning, a large number of tasks that previously had to be carried out manually can now be automated, along with increased quality and higher throughput.
Usecases
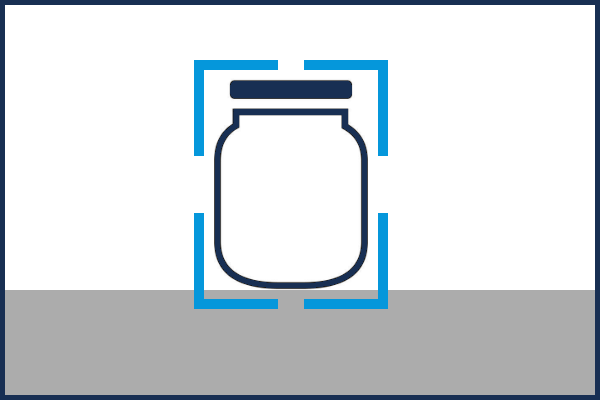
Detection
One or more objects can be recognized in a single image based on their appearance and features depicted.
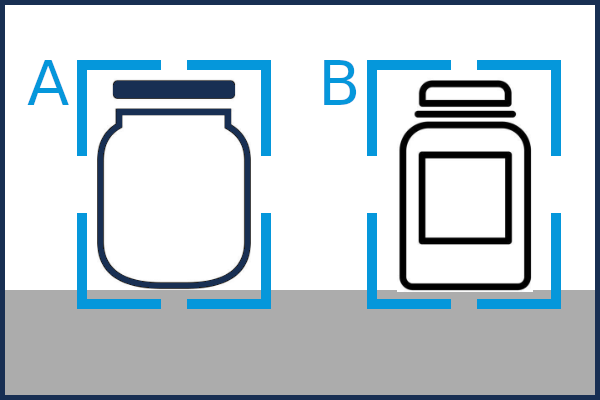
Classification
Detected objects can be assigned to one of many classes based on the characteristics detected,
Deviations from the norm can be recognized.
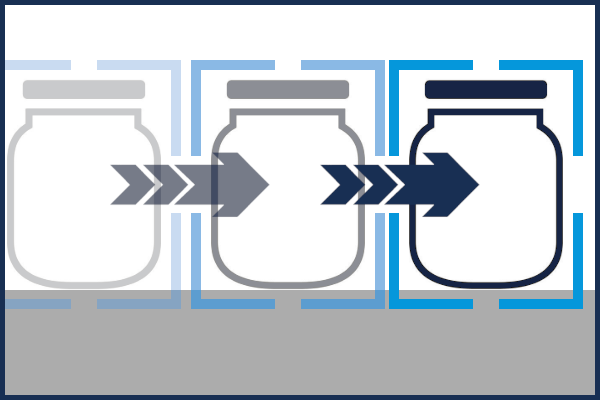
Tracking
By analyzing videos, objects can be tracked and counted, their speed determined, or anomalous/stable movements detected.
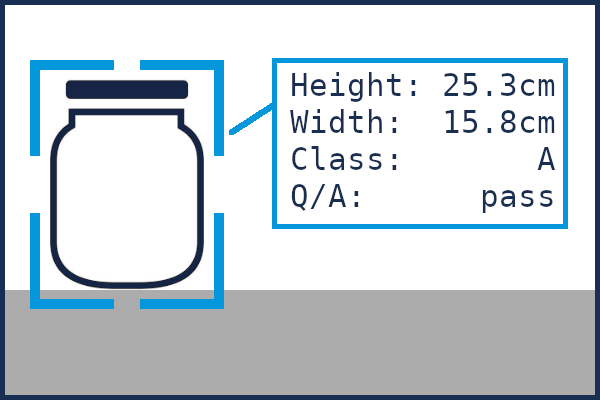
Measuring
Objects can be measured precisely – both the physical dimensions as well as their shape, color and possible defects can be measured with millimeter precision.
Procedure
With the help of the DTQ Vision Toolkit, we help you find, evaluate, and ultimately productively implement a solution to your computer vision challenge in a timely and cost-effective manner. Despite the almost inexhaustible possibilities of application areas and solution approaches, we follow a proven process model:
Requirement Analysis
In a requirements analysis, we develop and document the goals, requirements and framework conditions with you. We then plan a case study, which will result in a functional prototype.
Prototype
This prototype provides insights and reliable figures about the quality of the intended process.
During this phase the following steps are taken:
> Collection of representative data and its annotation (ground truth)
> Selection, training and evaluation of one or more suitable algorithms
Implementation
If you are satisfied with the results, we implement the procedures in productively usable programs and help with integration into any existing processes and infrastructures
Production
Of course, if desired, we will also accompany you in the productive phase with monitoring, further developments or any desired changes
Selection of previous Computer Vision projects
Here you will find a small selection of previous projects in various areas of application and problems.
A large number of projects have already been successfully implemented – both static cameras in industrial settings and moving cameras mounted in motor vehicles or on drones.
Depending on the application, a tracking algorithm tailored to the problem is used, which is adapted to the dynamic circumstances of the respective application. For example, cars and pedestrians can be recognized in road traffic, in an industrial setting, goods produced on the assembly line can be recognized, tracked, counted and analyzed for defects, free parking spaces in an area can be identified – as long as you can see a fact in an image/ can recognize video, the task can be automated through our DTQ Vision toolkit!
In this application, unsorted nuts, bolts and spacers run along a conveyor belt and need to be identified, classified and counted.
Due to the constant conditions (camera position, light, background, expected objects), a model-based method was used here. Here all variables can be modeled mathematically/physically and, on the basis of this, suitable classification methods can be implemented. This approach is often many times faster than deep neural networks and therefore requires fewer hardware resources.
The objects can be easily recognized and segmented against the uniform background. Since the distance of the camera to the assembly line and the calibration of the camera are known, the objects can be measured and classified photogrammetrically. The constant speed of the assembly line makes tracking easier.
The method was implemented in Python based on our DTQ Vision toolkit and runs on a commercially available Raspberry Pi.
When harvesting and storing organic foods, damage, unwanted stems, mold or disease can occur. Some of these impairments prevent a sale or can even jeopardize an entire batch.
Manual inspection and sorting is very time-consuming and labor-intensive, which is why automatic classification offers many advantages.
In this case study, a large number of images of lemons of different quality levels and with various of the impairments mentioned were recorded and annotated in color images. The images were (pre-)processed by the DTQ Vision toolkit and defects can now be detected and marked using a deep neural network.
The deep neural network is based on the Mask-RCNN structure and implemented in Pytorch.
Technology and Prerequisites
The basic requirement is a good idea of the challenge that needs to be solved.
In principle, every problem that can be imagined with Computer Vision can also be implemented –
We would be happy to support you in this phase
There are a lot of things to consider when selecting and installing hardware: Does the selected camera offer sufficient resolution and refresh rate as well as light sensitivity, is the lighting optimally set at the intended location, what performance indicators does the computer need? This varies depending on the application, but with our many years of expertise we can give you good, reliable advice.
When taking and selecting representative images/videos, it is important to recreate the later application as accurately as possible and to take all the necessary variables into account – if a machine learning algorithm is to be used, this is even essential.
There are also some pitfalls when annotating the data – we have long-standing partners who reliably create high-quality and cost-effective annotations in the shortest possible time.